製造業に携わる限り、工程の管理を行うことは避けては通れない必須事項です。
工程内管理を行う上で重要なのは、工程の検査を行い、後工程に異常品を渡さないことです。
「品質は工程内で作りこむ」という考えがありますが、この考えを形に出来る検査を「工程内検査」と言います。
今回の記事はこの「工程内検査」についてまとめていきます。
目次[非表示]
検査の目的
組織外で自社の不良が発生してしまうと深刻なダメージを負います。これを未然に防止するために「検査」を行い根本的な不良を取り除きます。
ー検査とはー
サービスや製品において測定・検査などを行い、規定要求事項(ISOの基準)と比較して、適合・不適合を判断する活動
サービスや製品において測定・検査などを行い、規定要求事項(ISOの基準)と比較して、適合・不適合を判断する活動
また上記の「適合」が示すものは規定要求事項を満たしている事であり、満たされているものを「適合品」、満たされていないものを「不適合品」といいます。
検査の実施対象は大別して以下二つとなり、判定対象も異なってきます。
・製品 :「適合品」「不適合品」
・ロット:「合格」「不合格」
ここで検査の目的について触れていきます。
検査の目的とは
安定かつ優れた品質を顧客に提供するために、製品が基準内に収まっているか評価し、その評価を関連部署にフィードバックを行い、工程改善につなげる事
検査というのは単に検査を行って「適合・不適合」、「合格・不合格」を提示するのが目的でなく、検査によって根本的な不良の流出を防ぐことが第一の目的となります。
検査の種類
検査を行う際に重要なのは、その時行わなければいけない検査方法を的確に選択し、正確に活用していく事が求められます。
上記を完璧にこなすことで、異常品の発生を押さえたり、不適合品の市場流出を防いだり、次工程からの信頼、市場からの信頼を得ることが可能となります。
この検査方法の種類は大きく分けて3つに分類され、さらにそこから細分化していきます。
大別すると「生産プロセス」「判定方法」「実施方法」のつに分類され、そこから「受け入れ検査」「官能検査」「全数検査」と言うように細分化されます。
細分化された検査方法は10個に分類されこれらを徹底することで良質な品質の確立へ繋がります。
品質管理における検査の種類についてまとめています。興味ある方は是非↓↓↓
検査方法の種類とそれぞれの特徴とは?QCにおける検査方法のまとめ
誰もが認める良質の製品を市場に流すためには「品質」と「検査」の組み合わせは切っても切れない関係です。 検査とは一概に言っても様々な種類があり、その時求められている「検査」を実施していく事が重要となります。 今回は品質管理における検査についてまとめてみました。 検査を行う際に重要なのは、その時行わなければいけない検査方法を的確に選択し、正確に活用していく事が求められます。 ...
今回の記事では生産プロセスの枠組みの中の「工程内検査」についてまとめていきます。
工程内検査とは
【工程内検査とは】
前工程から次工程に移動してもいいか判定するための検査の事
前工程から次工程に移動してもいいか判定するための検査の事
つまり完成に至るまでに工程間で行うことを指します。
受入検査は材料を購入して品質的に問題がないかチェックを行うのが「受け入れ検査」でその後材料を加工して、材料に何かしらの価値を追加して形や寸法が正しいことを確認を行い組み立て以降の工程に流していく事です。
工程検査には各工程間にその道に詳しい専任検査員を配置して検査する場合と、工程の作業感者が自ら検査する場合の二択になります。
この後者を「自主検査」と言い「後工程はお客様」を意識して不良品を流さないことを徹底することが大切となります。
マーケットイン・プロダクトアウト・後工程はお客様~QCの考え方①~QC検定【品質管理検定】
こんにちは。インコです。 前回の記事ではQC検定3級の実践分野の大まかな内容について説明させていただきました。 実践分野は計算問題がなく暗記のみとなるため復習が今まで以上に大切になってきます。毎日コツコツ継続していきましょう。 実践分野の内容と勉強法に興味がある方は↓↓↓ こんにちは。インコです! ...
工程内検査で検出される異常・不良というのは外部不良ではなく「内部不良」なので品質よりもコストの問題になってきます。
不良による製品の廃棄や製品の手直しなどの作業コストを削減していき事が重要となります。
品質管理と品質保証の違いとは?品質とコストの関係にも迫る QC検定攻略
皆さんは品質保証と品質管理の違いについて明確に答えることが出来ますか? 同じ品質でも「保証」と「管理」では大きく意味合いが異なります。 今回の記事はそれらの特徴から違いまで詳しくまとめてみました。 前回の記事では課題達成型QCストーリーについてまとめています。興味ある方は是非↓↓↓ ...
この工程内におけるコスト削減ですが、機械をその都度変えて見かけ上のコストに対応していくのはあまりに非効率です。
その時設備ではなく「人」にコストを変えていく事で解決する場合も多くあります。
しかし「人」を活用するには多くのリスクを抱えます。
そのリスクとは何でしょうか。
工程内のコスト削減には「人」を活用
前章ではコストは設備でなく「人」にかけるべきであると述べました。
しかし設備などの機械とは違い「人」は疲れや感情というのが要因として働いたりすることで「作業にばらつき」が生まれます。
これは仕方がないことですが、この「ばらつき」をいかに抑えるかがコスト効率の改善に繋がります。
労働者(人)の強みとばらつき
自動化が進んでいる設備主体で生産するラインには人のばらつきというのはそもそも生まれませんが、今ある「製造業」の多くはモノを「人の手」で作っています。
人はある程度の「型」には収まりますが機会と違って「物事を学習」していきます。
つまりコストをかけずに人は入れ替えが可能で作業を進めていくうえで自ら改善をしていきます。
最近よくCMで見かける言葉で「人間の本質はモノを考える事にある」というのがあります。
まさしくこの通りで物を考えてか、それを形にして、改善しより良いものを作りこんでいく。
この一連の流れがあるからこそ「今」があります。
これに対して設備を変更する場合には、多くのコストと時間がかかってしまいます。
あくまで一例として参考にしていただけたらと思います。
時間に対する費用対効果の「設備ー人」グラフを示しました。
設備はコストがかかるデメリットがありますが、導入直後から恩恵が得られ時間に対するコスパというのはほぼ一定になります。
しかし「人」はどうでしょう。
「人」を活用する場合、知識や能力は初めのころはほぼ0に近い状態です。
しかし時間がたつにつれて学習していく事で時間がたてばたつほど費用対効果というのは上昇していきます。
ものづくりの設備というのは長く使うのが基本となります。
なので結果として「人」をうまく育て活用することが一番効率的な作業法となります。
しかしメリットばかりではなくデメリットも存在します。
【作業者間のデメリット】
作業者間の作業ばらつきによる異常品の発生
作業者間の作業ばらつきによる異常品の発生
自分では理解していても、同じ工程の作業者にうまく伝わらず、理解してもらえていなかったらそれは「伝わっていない」という事になります。
この情報の不伝達により、作業者間にばらつきが生じ、結果として「異常品」を発生させてしまい、コスト効率へ影響を与えてしまいます。
その点機械は、一定の作業法で行いますのでそういった心配がないので一長一短といった所でしょうか。
ではこの問題を解決するにはどのような施策をするべきなのでしょうか。
ベテラン作業者を自身のロールモデルにする
先ほど「人」の費用対効果は時間経過に依存するというように述べました。
言い換えれば、早い時期から「人」を育てる事が出来ればその工程自体の底上げにつながり結果、高コスト効率を成し遂げられます。
それを成し遂げられるのはたった一つの戦法が以下になります。
ベテラン作業者を自身のロールモデルに
つまり熟練者をモデルにして真似るという事です。
例えばベテランと他の作業者の違いは何か、作業動作は何を意識しているのか、などを細かく分析をしていきます。
この事を「作業分析」と言います。
この方法は他の改善とは違って、目の前にすでに完成された姿が実現しているので、両者を比較していく事で違いが明確になります。
この違いの気づきというのを教育・拡散・訓練を行うことで工程内の底上げを図ります。
上の図はあくまで一例ですがこのような感じで伸びるんだという認識を持っていただければ大丈夫です。
工程内の自動化は必要ないのか?
今までの説明では設備投資を否定していて「人」のみ考えればいいというように見れるかもしれません。
しかし根本的に批判してるわけではなく、工程内の設備投資はある程度行うべきです。
特に「自動化」を行うことで「人」のばらつきをなくし、根本的な品質改善に貢献します。
この事から、定期的な自動化システムの導入、特に「不良自動検出器」などの活用をする事が工程に最大の効果を発揮します。ポカヨケ対策は治具と自動化でOK~ミスを防ぐ品質改善とは~
人間が何かに手を加える限り、この世に絶対というのは存在しません。 特に製造業では人間の感覚で作業をする場合が多々あり、それをいかに減らしていくかが重要となります。 多くの場合、人間が手を加える作業は何かしら不具合・ミスが生じる事を前提として考えらえ、そのミスをいかに防止するかが重要となります。 ...
不良検出器を活用し、少ない人員(熟練者)で工程作業を行うことがコスト面を見ればベストな方法と言えるでしょう。
まとめ
工程内検査は「後工程はお客様」を意識して行う
工程内検査は「人」「設備」のバランスを考える
いかがでしたか?
今回は検査のうちの工程内検査についてまとめました。
次回は最終検査です。それでは!
出荷検査の目的とは?最終検査の役割、重要性・信頼性について考える。
不良品が世に出回るか出回らないか、それをジャッジするのは受入検査でも工程内検査でもなく最終検査です。 この判断を誤ると、自身が想定していなかった大事になることは勿論、トラブルや多くの方々に迷惑をかけてしまう事態に見舞われます。 そうならないために最終検査はどういったことを意識して行い、また目的というのも明確にしていこうと思います。 ...
QC検定3級を楽して受かりたい方にお勧めです。
QC検定3級【品質管理検定】の合格率・難易度・勉強法のすべて
ものづくりに携わるうえでものづくりと品質管理という役割は切っても切れない関係なのはご存じでしょうか? 最近は品質の不正などの多発により「品質」への関心が集められています。 その関心と共に注目されている自己摘発が そこで今回の記事はQC検定3級をした自身の経験をもとに攻略法・勉強法をお伝えできればと思います。 Point.1 こんな人にお勧めです ・勉強時間が足りないから要領よく学びたい ...
ブログランキング参加しています!

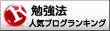
勉強法ランキング
FC2 Blog Ranking
0 件のコメント:
コメントを投稿