改善活動において一時の成果で終わらない様に維持管理を行うことは重要な事ですが、それら管理の効果を最大限活かすためには基準を定めておく必要があります。
この事を標準化といい製造業などでは基礎の「き」として広く知られています。
一般的にすでに知れ渡っている事もあり標準化=ルールという漠然とした意味で理解されている方も多いかと思います。
そこで本記事では標準化の目的から作成ポイント、社内標準化・工業標準化などについても分かりやすく解説していきたいと思います。
前回の記事では方針管理と日常管理についてまとめています。興味ある方は是非↓↓↓
方針管理と日常管理とは?違いや関係について分かりやすく解説
企業において、会社業務を管理するうえでは方針管理と日常管理に大別されます。 これら管理には一見親和性がないように見えますが意外と関係があるものになります。 本記事では企業運営における方針管理と日常管理の違いや関係についてまとめていきます。 ...
目次[非表示]
標準化とは
標準化には新旧で定義の長さが異なります。
新標準化・旧標準化のJIS定義について比較して見てみましょう。
ー新標準化【JIS Z 8002:2006】-
標準化とは実在の問題または起こる可能性がある問題に関して、与えられた状況において最適な秩序を得る事を目的として、「共通にかつ繰り返して」使用するための記述事項を確率する活動
ー旧標準化【JIS Z 8101:1981】-
標準を設定し、これを活用する組織的活動
標準化とは実在の問題または起こる可能性がある問題に関して、与えられた状況において最適な秩序を得る事を目的として、「共通にかつ繰り返して」使用するための記述事項を確率する活動
ー旧標準化【JIS Z 8101:1981】-
標準を設定し、これを活用する組織的活動
お分かりいただけたでしょうか。新標準化・旧標準化を比較すると新標準化はかなり詳しく述べられています。
しかし新標準化のJIS定義では補足として、廃止された旧標準化についても載せられています。この事から旧標準化の方が理解しやすいというのが分かるので新標準化が長くて覚えられないという人は旧標準化を覚えておきましょう。
因みにここでいう標準とは以下のようになります。
ー標準とは【JIS Z 8101:1981】-
関係する人々の間で利益または利便が公正に得られるように、統一化・単純化を図る目的で、物体・性能・能力・配置・状態・動作・手順・方法・手続き・責任・義務・権限・考え方・概念などについて定めた取り決め。
測定に普遍性を与えるために定めた基準として用いる量の大きさを表す方法又は物。
関係する人々の間で利益または利便が公正に得られるように、統一化・単純化を図る目的で、物体・性能・能力・配置・状態・動作・手順・方法・手続き・責任・義務・権限・考え方・概念などについて定めた取り決め。
測定に普遍性を与えるために定めた基準として用いる量の大きさを表す方法又は物。
標準は言い換えれば「基準」とも表すことが可能であり「標準化=強制」というイメージがありますが、品質管理場度の場合は「標準化=任意」と考えることもできます。
これまでの事を踏まえて標準化についてまとめてみます。
標準化とは全社一丸となって仕事に向き合い、効率的かつ効果的に品質向上を掲げ、基準化と単純化をを行って結果に示すこと
因みに国際標準化機構(ISO)においても標準化について述べています。
補足までに紹介します。
ー標準化【国際標準化機構】-
実在の問題、起こる可能性がある問題に関して与えられた状況において最適な秩序を得る事を目的として、共通にかつ繰り返して使用するための記述事項を確立する活動、また規格を作成し実施する過程からなる
実在の問題、起こる可能性がある問題に関して与えられた状況において最適な秩序を得る事を目的として、共通にかつ繰り返して使用するための記述事項を確立する活動、また規格を作成し実施する過程からなる
この時規格とは与えられた状況において最適な秩序を達成する事を目的に、共通にかつ繰り返して使用するために、活動又はその結果に関する規則、指針又は、特性を規定する文章であって合意によって確立し、一般に認められている団体によって承認されているものとされています。
この規格というのは大別して以下二つに分類されます。
・公的機関
・マーケット
日本工業規格や国際標準化機構などの公的機関による作成された規格をデジュールスタンダード、市場など絵起用される標準の事をデファクトスタンダードと呼ばれています。
そもそも標準化のねらいというのは規準化や単純化を図るものではありません。
顧客に満足を与え社会に貢献するという企業目的に沿った活動を維持し、その先の発展を目指していくためには生産能力の向上、簡潔にまとめると利益を追求し確保する事はとても重要となります。
この生産能力の向上が標準化の真の狙いです。
それでは製造現場における標準化による生産能力の向上はどういったメリットがあるのでしょうか。
1)作業時間の短縮
2)異常品の減少
3)エネルギーの抑制
他にも多々存在しますが、一般的になじみ深いのは上記かと思われます。
これらは一貫して作業方法の標準化を図る事で達成する事が可能となっており、たった一つの標準化で3つの事項が改善されるなら標準化はやはり率先して行うべきでしょう。
標準の種類
標準は単に「すべての基準」というくくりではなく、その企業・部署・部門ごとに様々な標準が存在します。
1)作業標準
2)業務標準
3)品質標準
作業標準に関して言えば、この標準は品質部門や実際の現場で作成する事になります。
もし標準の変更がある場合は作成した部門が責任をもって改定を行うか、承認を行いましょう。
現場で手掛けた標準は、作業者が効率よく作業を行うための物なので作業者が自分たちで改定しても大丈夫ですが、この場合も上司の許可などはとるべきでしょう。
生産現場における標準
前章における生産現場で最も重要な標準は作業標準だと言われています。

作業標準の目的
作業標準の目的は大別して二つに分類されます。
・作業効率の向上
・問題の早期解決
作業標準の一つ目の作業効率の向上に関しては、作業標準について知見がある人・もしくは教育を受けているものであれば、効率的かつ効果的に行える作業を定めます。
この作業を職場に浸透させ定着し維持してもらう事で、QCDを確保することが出来ます。
また仮に異常が起きた時は問題の早期解決また原因の浮彫を容易にします。
問題が発生したときは作業標準を適切に順守していれば問題発生の焦点を絞ることが出来ます。
しかし作業標準が確立していないと対策が遅れる事に繋がります。
作業標準のPoint
標準を作成しても作業者が守らない事には意味を成しません。
標準を作成した際にどのようなpointを押さえておくべきなのでしょうか。
作業標準のPoint
1)明確な目的の確認
2)要因×結果を明白に
3)誰でも理解できる内容に
4)現実的な標準の意識
5)100%の標準でなくていい
6)重点思考で作成する
7)自己満の内容にしない
8)あらかじめ対処の検討
9)改善後の改定を意識する
1)明確な目的の確認
2)要因×結果を明白に
3)誰でも理解できる内容に
4)現実的な標準の意識
5)100%の標準でなくていい
6)重点思考で作成する
7)自己満の内容にしない
8)あらかじめ対処の検討
9)改善後の改定を意識する
まず初めに行動を起す際には明確な目的の確認は欠かせずこれは標準作成にも当てはまります。
なんの作業の標準なのか、何故標準を作成するのか、標準化した後はどうするのかなどある程度広い視野で目的の確認を行います。
目的が決定したら要因と結果を明白にします。
これは品質特性を得るための作業方法を具体的に示すことを指します。
例えば「体脂肪率を5%落とすこと」というのを目的として置いた場合、「筋トレを1時間行った後に20分有酸素運動を週に3回行って体脂肪率を5%落とす」ことのような詳細まで明記していく事が重要となります。
もし作業標準を品質特性(目的)のみで示した時、作業者は自身でやり方を工夫しなければなりません。
詳細を明記する事でばらつきの発生を抑制する事に繋がり、詳細を明記する事で誰でも理解できる内容に繋がります。
「標準」という文字はイメージ的には「守らなくてはいけない」という堅いイメージがあるかと思います。
しかし作業標準は技術的には完成形でなくても問題はありません。
大切なのは現実的な標準の意識を確立することです。
標準の意識さえあれば100%の標準でなく、長い目でみていいものへ変えていくアプローチが重要となります。
初めから無理難題な標準を定めるより、段階的に改善されていく方がモチベーションも維持でき、最終的に完全な作業標準が完成します。
作成する際は重点思考で作成していく事で無駄な標準を省く事にも繋がります。
また作成の際には作業に関係する人たちが納得する内容を心がけましょう。
自己満な内容にならない様に全員の理解を得た内容にすることで継続的な標準を確立する事が出来ます。
最後に「今」だけでなく「未来」を見据えた標準を作成していきます。
組織は営利目的で活動している以上、ニーズに合ったものを実現していく必要があります。
特に作業現場はその影響をもろにうけ、設備・材料などがその都度変化するでしょう。
そういった時にあらかじめ条件が変わった際の対処の検討をしておくことで実際にその状況に陥った時、スムーズに対処する事が可能となります。
またより良い作業法を発見した際は改定する事になるので改善後の改定も意識する事が重要となります。
作業標準の注意点
作業標準はやり方を統一する事が主な目的なので前述した通り、経済的かつ現実的なものを意識して作成していきます。
この経済的かつ現実的な作業標準を実現させるために以下の6つについて注意して作成していきます。
作業標準の注意点
1)使用した部品・原材料の明記
2)利用設備・治具の明記
3)作業の方法・手順・条件の明記
4)注意点の明記
5)正確な作業時間の明記
6)問題発生時の対処法の明記
1)使用した部品・原材料の明記
2)利用設備・治具の明記
3)作業の方法・手順・条件の明記
4)注意点の明記
5)正確な作業時間の明記
6)問題発生時の対処法の明記
作業標準を作成するにあたり、誰でも理解しやすく、実行できる標準を作成するためには、使用した部品・原材料の明記は勿論、利用設備・治具の明記まで詳細に明記していきます。
この時、検査規格や購買規格・設備管理規定などの各決まりについて調べる事が必要となります。
そして一番と難所ともいえるのが作業方法・手順・条件の明記です。
書き方はその企業・現場によって異なってくるとは思いますが、品質基準と作業pointの関係などは明確にし、また数値化していく事が重要となります。
作業pointに関しては手順に関することだけでなく、不適合品が発生する場合、異常が発生する場合などの注意点の明記しておくと作業者は少なくともそこに書いてある事は行動には移さなくなります。
またその標準された作業はどれくらい時間を有するのか正確な作業時間を明記しておくと作業者自体の予定が立てやすくなります。
最後に仮に問題が発生した場合には誰に連絡をして、どのような応急対策を施せばいいのか問題発生時の対処法を記しておくべきでしょう。
社内標準化
前章では生産現場の標準について述べさせていただきました。
それではもう少し規模が大きくなった標準化について触れていきます。
生産現場より大きな規模の標準化には社内標準化・工業標準化があります。
まず初めに社内標準化についてまとめていきます。
社内標準化の目的
確実に守られる・実施される標準化を確立する事で、「コスト低減」「技術力の向上・蓄積」「品質の向上」などを目的として作成される
確実に守られる・実施される標準化を確立する事で、「コスト低減」「技術力の向上・蓄積」「品質の向上」などを目的として作成される
社内標準は組織内のあらゆる活動の簡易化、効率化を目指して作られるものであり、国際規格や国家規格にも整合していることが必要とされます。
また上記「社内標準化の目的」内のコストの低減は重要な項目の一つとされており、以下項目が挙げられます。
・業務をルール化する事による効率の向上
・材料・部品の標準化による互換性の向上
社内標準化の成果である社内規格・標準はコストの削減につながる互換性の向上や品質の向上、技術の蓄積にも貢献します。
社内標準化の進め方
社内標準化は次の4つのプロセスで進めていきます。
社内標準の4つのプロセス
1)社内規格・社内標準の作成
2)上記業務の実施
3)結果の確認
4)社内規格・社内標準の見直し
1)社内規格・社内標準の作成
2)上記業務の実施
3)結果の確認
4)社内規格・社内標準の見直し
社内標準・社内規格を作成する際は上位規格とされる国際規格や国家規格との関係がある場合は、内容的に矛盾が生じないよう整合性を保持する事が不可欠となります。
自社が所有する技術レベル、生産現場のレベルを考慮して守ることが出来る事。また確実に実施できることが重要となります。
また作成された規格・標準に基づき実際に行動に移します。
実施する前に教育・訓練を行ったうえで実際の作業を行うのが最も効果的な標準の活用となります。
実施した標準の行動結果について効果の確認を行います。
標準化は正しかったか、修正点はないかなどの考察をする事は勿論、定期的にこの確認を行い陳腐化を防ぎ社内の技術レベルの向上に結び付けていきます。
もし成果が得られなかった場合は、何故成果を上がられなかったのかという視点から、1から標準の規格や教育についての見直しを行います。
またこの標準化から始まる管理のサイクルの事をSDCAサイクルといいます。
PDCA・SDCA・PDCASサイクルと維持管理と改善について具体例と体験談を用いてわかりやすく解説
皆さんは働くうえでどのように維持管理を行っていますか? 常に目標を設定し問題を解決していく事を繰り返すことで、高い水準の管理活動を維持することに繋がります。 そこで今回は維持管理の基本である「維持管理と改善」「PDCA・SDCA・PDCAS」についてまとめていきます。 前回の記事で顧客満足についてまとめています。興味ある方は是非↓↓↓ ...
社内標準化の種類
社内標準化は以下の3種類に大別されます。
規定
全社に共通に運用していく総括的かつ横断的なもの。規格
技術的な要件などの規格値や基準値などが具体的に定められているもの。社内標準
組織内において製品・材料に関して、生産・購入などの業務用途で企業が独自に作成する物。工業標準化
工業標準化とは鉱業分野の標準化を指し、国が定める工業標準としてJISが選定されています。
日本の工業標準化における制度は工業標準化法に基づいたJISの制定と適合性に関する制度の二本柱から成り立っています。
工業標準化の目的
1)生産の効率化
2)技術レベルの促進
3)社会活動の利便性の確保
4)消費者利益の確保
1)生産の効率化
2)技術レベルの促進
3)社会活動の利便性の確保
4)消費者利益の確保
日本工業規格(JIS)とは
工業標準化法に基づく鉱工業製品に関する国家規格の事を言います。
JISはJapanese Industrial Standardsの頭文字をとって略称で呼ばれています。
因みに医薬品・化学肥料・農業などはJISの対象外とされています。
JISマークの種類
JISマークは登録機関から認証を受けた事業者が製品などにJISマークを表示することが出来る制度の事を言います。
このマークがあれば第三者的に品質が保証されていることになるので信頼に繋がります。
このJISマークには以下3種類があります。
・鉱工業用
・加工技術用
・特定側面用
国際標準化活動
国際標準化とは、国際的に・多数の国々が協力して合意を重ねる事により国際的に適用される国際規格を制定し、普及する事によって進められる標準化の事を指します。
国際標準化の代表的な機関として有名なのがISO(国際標準機構)になります。
まとめ
作業標準のPoint
1)明確な目的の確認
2)要因×結果を明白に
3)誰でも理解できる内容に
4)現実的な標準の意識
5)100%の標準でなくていい
6)重点思考で作成する
7)自己満の内容にしない
8)あらかじめ対処の検討
9)改善後の改定を意識する
1)明確な目的の確認
2)要因×結果を明白に
3)誰でも理解できる内容に
4)現実的な標準の意識
5)100%の標準でなくていい
6)重点思考で作成する
7)自己満の内容にしない
8)あらかじめ対処の検討
9)改善後の改定を意識する
いかがでしたか。今回は標準化についてまとめてみました。
次回はQCサークルについてです。それでは!
QC検定3級を楽して合格したい方にお勧めです!小集団活動(QCサークル)の目的と進め方について、例を用いて分かりやすく解説
企業という枠組みの中で、マネジメント層以外の人たちが行う活動とは何があるでしょうか。 営利目的で活動していく限り、継続的改善活動は無くてはならない取り組みであり、これは特に一般従業員が積極的に行っていく事が重要となります。 この取り組みの一つとして挙げられるのが小集団活動といいQCサークルと略称されています。 本記事では小集団活動のQCサークルの目的と進め方についてまとめていきたいと思います。
ブログランキング参加しています!QC検定3級【品質管理検定】の勉強方法・勉強時間を公開。3か月で9割を獲得するための対策とは?
ものづくりに携わるうえでものづくりと品質管理という役割は切っても切れない関係なのはご存じでしょうか? 最近は品質の不正などの多発により「品質」への関心が集められています。 その関心と共に注目されている自己摘発が そこで今回の記事はQC検定3級をした自身の経験をもとに攻略法・勉強法をお伝えできればと思います。 Point.1 こんな人にお勧めです ・勉強時間が足りないから要領よく学びたい ...

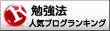
勉強法ランキング
FC2 Blog Ranking
0 件のコメント:
コメントを投稿